装置工作の展示室 廃材リメイクをメインとした自作の装置を展示しています
<展示内容> 見たい項目をクリックしてください。 
@帯鋸の送り受け台
欲しかった帯鋸(1尺一寸引き割り)を購入しました。
長尺物の引き割りの場合、受け台及び送り台が必要になりますが、市販品を購入すれば7〜8万円の負担になります。
機能は多少、不自由でも予算節約のため自作しました。
材料は農業用アルミローラ(L=150cm、W=30cm、ローラピッチ=10cm;約2万円)、軽量鉄骨材(廃品)、アジャスター用
ボルトナット(約400円)です。
軽量鉄骨は近所の人が物置小屋を解体した際に戴いたものをオンボロ高速切断機で切断し、家庭用電気溶接機で
オンボロ技術によって溶接しました。
アルミローラは送り側用に90cm、受け側用に60cmとして切断し、アルミサッシュフレーム廃材で補強しました。
アルミローラ部と架台はステンレスボルト(廃材)で連結しました。
架台には移動用に小型キャスター、レベル調整用のアジャスターを取り付けています。
更に、小物(1m以内くらいの)の切断には受け台だけで良く、頻繁に使用することを考慮して帯鋸本体へ組み込み、
アジャストフリーで使用できるようにしました。→(組み込み受け台)
これも廃材の軽量鉄骨を使いました、ローラ−は昔のドットインパクトプリンターの紙送りゴムローラーをリメイクしました。
昔のプリンター部品は凄くタフに作ってありますから、十分に加重に耐えています。
購入時に付いていた木製台は粗末なため撤去し、替わりに樫材で自作した台を取り付けて移動用の大型キャスター
も付けました
以下に画像を示しました。
送り台 |
受け台 |
本体組み込みの受け台との組み合わせ |
組み込みの受け台
(収納状態) |
|
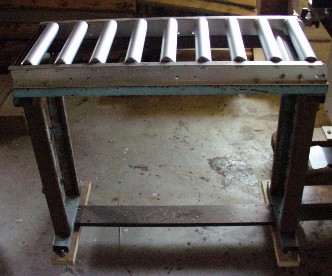 |
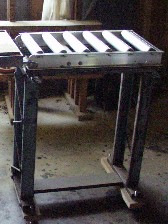 |
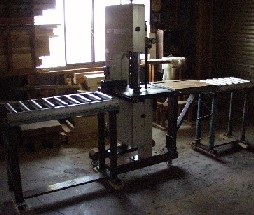 |
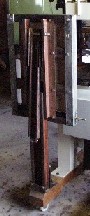 |
|
<展示内容に戻る>
A遠心型排風機とドロップボックス型サイクロン集塵機
概要)
市販の排風機を探しまくりましたが、遂に適合するものが見当たらず自作することにしました。
排風の次には集塵機となる訳で、これはサイクロン式の中でも最もシンプルで低圧損で定評のある
ドロップボックス式を採用しました。
ドロップボックスは低圧損というメリットはありますが、微細な粉塵はトラップできないというリスクがあります。
幸いにして工室の周囲が私有地であり、多少の超微粉はよかろうという反環境的な甘い判断でもって排風機
の能力を自愛しながらの設計と相成りました。(最終的には水中でトラップする手法を考えていた)
排風機の動力は100V-300W以下の制約(リミッターの関係)がありまして、これには20年前に休止していた井戸
ポンプのモータを再利用しました。→松下電器、深井戸用(100V240W、コンデンサ誘導型)、3780rpm。
軸受け部はマッサージ器のベアリングと運搬機の軸受け、軸はステンレス製の長軸ボルトを使用しました。
プーリはマッサージ器のものを、Vベルトは昔の車のファンベルト予備品(当時、新品のもの)、ファン及びケーシング
はVC廃品であるフランジとパイプをリメイクしております。
ドロップボックス本体は風呂ボイラーの灯油タンクをリメイクしましたし、100%近い領域に於いて廃品を再利用
しております。
吸引ダクトはY字型接続に因る2系統としています(接続バンド等は全て自作)。
試運転の結果、予想以上の能力に感動!!
減圧度と排風量を測定したいのですが測定器がありませんので、何時かの機会に。
遠心型排風機の製作
羽根車には沢山の種類があり夫々の長所と短所のバランスで選択することにしました。
今回は遠心型ターボファンというもので、掃除機に採用されているものの親戚です。
空気にも質量がありますから円盤を回転させると遠心力が作用して空気は外側に流れます。
よって円盤の中心部には負圧が、外周部には正圧が生じます、このとき効率良く空気を掴むために羽根があるわけです。
公知文献では以下の左図ような構造で示されています、今回は硬質塩化ビニルで作成していますので右図のように
グロテスクな形になりました。
ここで最も苦労したのはバランスでした、図面どおりにカットし組み立てたのですが僅かな誤差とか接着剤偏りがバランス
に影響しました。
実際には中心部に軸を通して両側にベアリングをセットして手で回転し停止位置がランダムになるように各羽根を削り、
バランスを調整しました。 羽根車のサイズは直径235mmです。
文献より |
羽根車の側面 |
羽根車の斜面 |
羽根車の上面 |
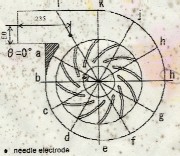 |
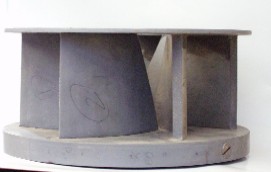 |
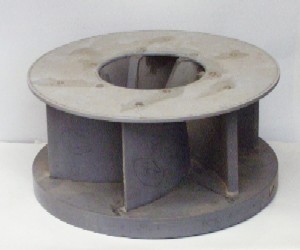 |
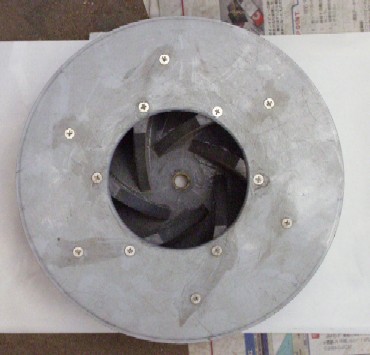 |
ケーシングも以下の図に示したように全て硬質塩化ビニルで製作しています。
左図は羽根車を取り付ける前のケーシングの状態で、次がセットした状態で駆動軸はケーシングのセンターよりずらした
状態になっています。ハウジングのサイズは直径280mmとなっています。
右図は吸引側をセットした状態です、回転状態を見るために5mmのアクリル板(MMA)を採用しています。
又、排風機の振動を吸収させるために厚さ6mmのゴムを各接合部にはめ込んで共振を極力おさえてあります。
ケーシング空の状態 |
羽根車取り付け状態 |
排風機全体(駆動部は下部) |
排風機の駆動部 |
|
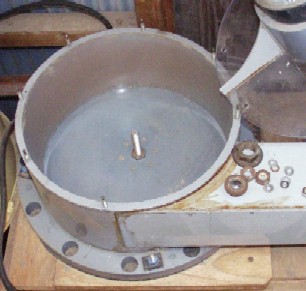 |
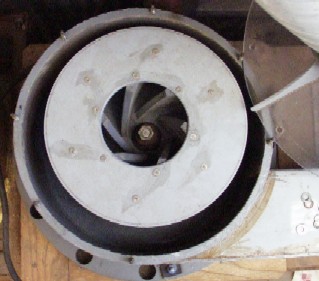 |
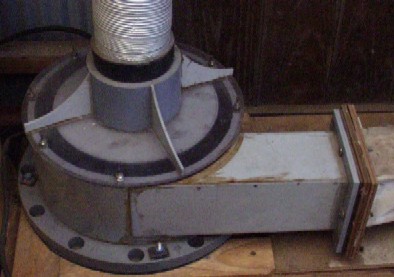 |
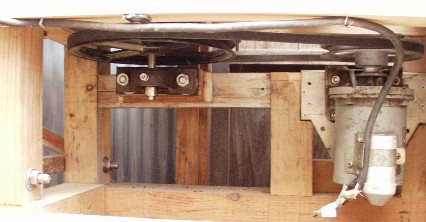 |
|
さて羽根車の運転速度ですが、モーターが3780rpmでプーリー減速比が145/255ですから2149rpmと計算されますので、
大体2100rpmくらいの速さで回転しているものと思われます(実際には負荷がかかるのでこれ以下)。
無負荷時の吸引力は凄まじく家のサイクロン掃除機の3台分くらい?の感じでした。
ドロップボックス型サイクロン集塵機の製作
スペースの関係、コーン部材料が無かったこと、排風機の能力不足などの関係で、ドロップボックス型の集塵機に決定しました。
このタイプは微粉の集塵能力に難はありますが、圧損が極めて少ない(半分以下)メリットがあります。
(コーン型サイクロンの圧力損失は1.1〜1.5KPa、ドロップボックスのそれは0.64KPaとの報告がある)
幸いにして以前に使っていた灯油ボイラーのタンクがありましたので、これをリメイクしました。
タンク下部の切除してファイバードラムの蓋に排出ダクトパイプと覗き窓を取り付けてバンドで固定しています。
側面には吸入ダクトを円周方向に取り付け、これ等の接合部には全てシリコンコーキング剤を充填し機密性を保持しています。
底部(タンク時には上部)には集塵物の取り出し口(ゴムシール付き)を取り付けて蝶ナットの操作で簡単に取り出せる。
又、中心部のケー゛ジ部には傘型セパレーターの軸ボルトが取り付けてあります(中央図)。
ドロップボックスのサイズは直径400mm、高さ735mmで申し分の無い大きさです。
ドロップボックス全体 |
ドロップボックス底部 |
ドロップボックス吸排部 |
|
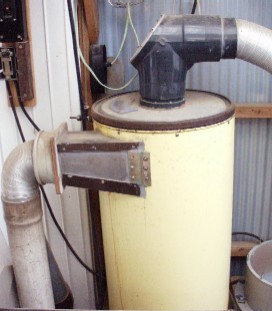 |
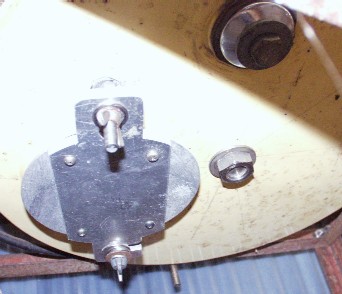 |
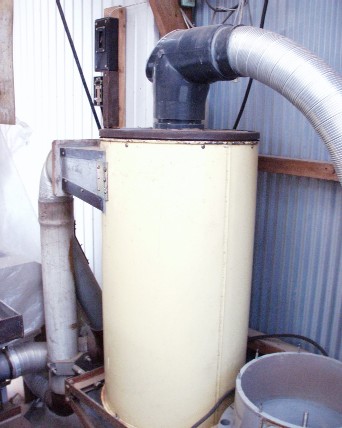 |
|
ドロップボックスの吸排部は右写真の如きで、曲がりの部分はアルミフレキシブルパイプを使い圧損を極力おさえています。
吸入側の分岐は可能な限り分岐角度を浅くとったY型構造とし、90度分岐の1/3以下の圧損に抑えてあります。
実際に運転してみますと圧損はかなり感じられるものの吸引力はかなりのもので帯鋸運転時の粉塵は殆どありませんでした。
丸太などの引き割り時にはテーブルとの間隔が開きますから制御風速が低下し粉塵が立ちます。
この対策としてY型分岐した一方のダクトからテーブルの上面を吸引するラインを設置していますが吸引力は今一でした(残念)。
通常は角材の引き割り作業が殆どですからこのラインには盲蓋がしてあり、帯鋸の下部吸引のみとなっています。
モーターの出力の割には優れた吸塵能力が得られたこと、排風機内部の微粉付着と排気口付近の状態からドロップボックスの
トラップ能力は予想以上に高く再処理の必要は無いと判断しました(民家からも遠いし)。
課題は排風機の耐久性???である。
因みにドロップボックス上面の覗き窓は静電気に起因すると思われる微粉付着で本来の目的(集塵確認)を達成できなかった。
<展示内容に戻る>
Bパラボラ型ソーラークッカー
概要)
原油高、森林保護、温暖化対策と言いつつ、本当は貧乏対策で地球に無尽蔵に降り注ぐ太陽エネルギーを戴くことにしました。
と言いましても市販のソーラークッカーを購入したのでは面白くないということで、恒例により廃品を利用した自作を
計画しました。
半年かかって材料集めをやり、農業の合間を盗んでチマチマと製作に着手した次第です。
放物面鏡は、安全のため焦点が凹面内におさまる必要があるので、直径1.4mの開口面の内側に焦点が来るように設計する。
原点に頂点を、y 軸上に焦点をもつ放物線を考えると、その焦点距離f
はy=ax2 のときf =1/4aである。
放物面をエクセルで計算し焦点距離30cm、直径140cmの型紙を作成し自転車のリムを成形して骨格とし、それに
流し台とか浴槽のステンレス板をカットしてハンドリベッターでくっつけた(結果的には焦点距離は33cmだった)。
(ここでの焦点は物理学的な明快な焦点ではなく約20cm程度の楕円状に集光するブロードなもので
実はこれが重要であり、調理を目的とした集光としてはピンポイントより理想の集光状態といえる。)
最も苦労したのは仰角調整機構であった。
仰角調整機構としては幾種類かの公知の手法があるが、手持材料の不足とフレーム強度不足などの理由で最も細工が難しい独自の
機構を考案してしまった。(特許性もある手法だがこれが後の五徳構造を複雑なものにしてしまった)
仰角調整は車ジャッキのようなメカニズムであるが構造上の工夫がしてあります、長尺ボルトは建築用のアンカーボルトを
ダイスで加工して両端をボールベアリングで固定しています。
その結果、調整は非常にスムーズで片手で精細に行えます。
台座は当初、木製でしたが安定性向上と強度upのために金属製に変更しました、これも全て廃材です。
(方位角回転部はコンクリートミキサー廃品、その台座は車のホィール、その他も各廃材を利用した)
パラボラの裏側 |
迎角調整部 |
|
五徳の構造 |
湯沸し風景 |
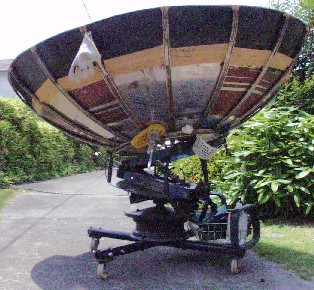 |
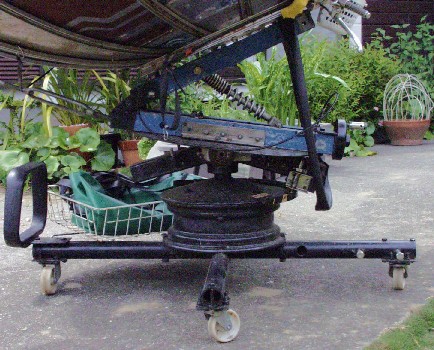 |
|
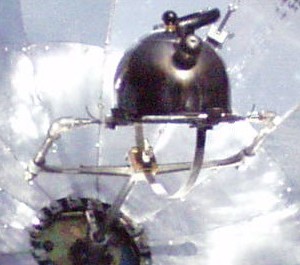 |
 |
クッカーの性能を左右する反射板に関して確認テストを実施した。
各金属の赤外線反射率はAg(98.9%)、Al(93.9%)、Au(98.2%)、Cu(98.5%)である。
ステンレスはFe、Ni、Crの合金でありNiに近いといわれているので72.0%とかなり低い値である。
現行のステンレス板に家庭用アルミフォイルを仮接着して反射効率の違いを確認することにした。
8割程度の面積をアルミで覆って太陽光を受けてみたところアルミ被覆の部分はヒンヤリした低温で、ステンレス部分はいつものように熱かった。
これだけでも反射効率の改善が窺えるが、実際の湯沸しテストでも飛躍的な結果を得た。
今まで1.5L沸かすのに30〜40分かかっていたが20〜30分で勢いよく沸騰した。
改めてAlの反射効率の良さを確認できた。
尚、ある文献によると酸化して白っぽくなったAlでもそれほど反射効率は低下しないと報告されている。
(しかし其の後の運転でかなり反射率が低下している結果を得た(2割は低下)、文献は嘘である模様)
今後、ステンレス板の上にアルミ板もしくはアルミ箔を接着する予定。
酸化防止用のコーティング剤を塗布する必要があるが、現在検討中(シリコン系かテフロン系だろう)。
ただ一年近く経過しても1.5Lの水は30分くらいで沸騰するので、或る意味では過剰性能かも。
今後の課題
最も煩わしいのは迎角と方位角の調整である、調整を怠ると集熱がずれて大変なことになる。
やかんのハンドルと笛吹き部を焼損(溶融)させてしまった。
自動追尾装置を考えているがどうなることやら。
ま、あまり先端技術を取り入れてトラブルを増発させるよりスローなリズムで楽しむ方が得策かも知れない。
もっと泥臭い手法で改善し煩わしさを軽減するのが良いかもね。
<展示内容に戻る>
C木工旋盤
概要)
木工旋盤は以前より垂涎の木工機械であったが、頻度が低い割りに高価であり購入に至らなかった。
今回、精米機の廃品を眺めているうちにムラムラメラメラと自作の虫が湧き出てきた。
当初はチャックなどの高精度の箇所は購入する予定であったが、全て自作するという欲望に勝てずに遂に精度を
度外視することに決着した。
このことで後々、難儀するとも知らずに製作をスタートしてしまった。
駆動軸、軸受け、そのハウジングは精米機のリメイク、チャックは4つ爪チャックを硬質塩化ビニルを主体とした材料で
芯押し台と共に製作した、悪戦苦闘の気が狂いそうな日々であった。
駆動モーターは洗濯機の廃品と類推されるコンデンサ誘導型モーターで正逆転のさせる回路を組んだが、一発で切り替える
ロータリーSWが入手できず仕方なくスナップSWを4個組み合わせて誤魔化した。
製作には足掛け1年を費やして(材料切れの関係が主因)完成した(試運転せずして完成か?)。
全体正面 |
全体上面 |
チャック&芯押し部 |
電源&反転SW部周辺 |
|
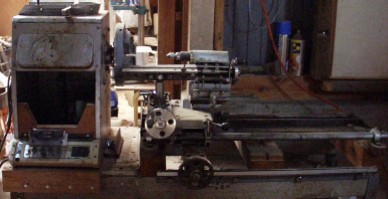 |
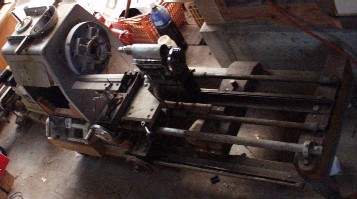 |
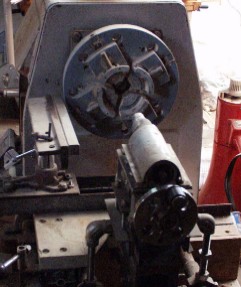 |
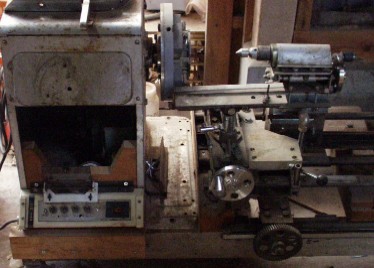 |
|
試運転は切削バイトの柄(藪椿材)を4本制作したが、満足行く結果であった。
次は何らかの作品を作る予定。
<展示内容に戻る>
Dドリル研磨機
概要)
穴あけ作業ばかりしている訳ではないが鉄工ドリルをかなりの頻度で使用している。
鉄工ドリルは高価で、特に大きいドリルは滅多に購入できないほど高価である。
今まではグラインダーでいい加減に研いでいたが、特にサイズの小さいものは先端角と逃げ角が無茶苦茶になる。
ドリル研磨機の市販品はあるが、とても高価でありドリルが何本も買える値段、えーいっとばかりに自作に踏み切った。
云うまでも無く全て廃材のリメイク、リサイクルである。
多少の使い難さもあるが概して満足いく使い心地である。
側面にぶら下がっているのは先端角ゲージである(無論、自作品)
<展示内容に戻る>
bb
|